Pressure Transmitter with Parylene Coating for Extreme Environments
For the use in seawater or with aggressive media, Baumer’s product segment Process Instrumentation offers pressure transmitters with Parylene coating protecting against corrosion and increasing the life cycle of the measuring devices. Especially in applications of over- and underwater shipbuilding, the sensors have to be resistant against seawater.
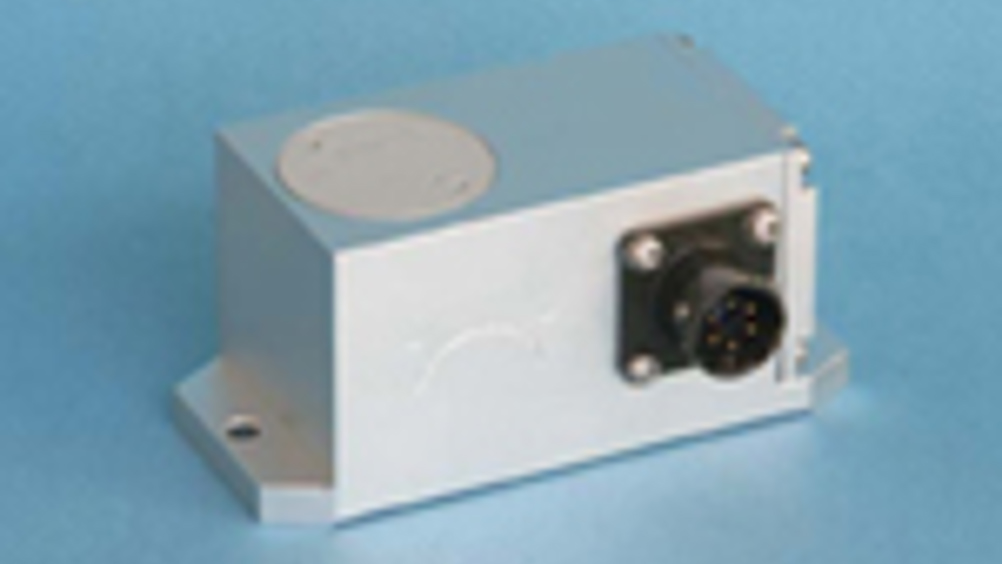
Baumer produces its pressure sensors with metal thin film membranes made of high-quality stainless steel. For applications in seawater or with aggressive media, the membrane and the sensor parts contacting the media should be additionally protected against crevice corrosion. Due to its excellent protective skills, Parylene C is a suitable material for this. The abrasion-proof coating is rugged at a continuous operation temperature of up to 150°C, resistant against fungal decay and chemicals and persistent to radiation. Additionally, it provides an excellent electrical insulation with high disruptive strength. From a coating thickness of only 0.2 µm, the material is completely free of pores. Since there is no gas emission with Parylene C, it is also suitable for the aerospace industry and approved by the NASA.
Compared to conventional coating methods, Parylene C enables an evenly thin and of pore-free coating even in joints and hollow spaces. Internal coatings of pressure connections with capillary supply, as for example with the PDR transmitters used for shipbuilding can be realised.
The coating of a pressure sensor membrane takes place as batch fabrication under vacuum. Due to the gentle production process and the very thin coating of 1 to 50 µm, the sensor’s features like linearity and hysteresis are not impaired.
The Parylene coating is optionally available for all pressure sensors. Baumer especially recommends it for applications in extreme environments in order to increase the sensors’ life cycle. Generally, any material can be coated with Parylene to protect it against corrosion.