At the cutting edge
A surface hardening technique could eventually lead to a plastic-bladed scalpel. Lou Reade reports
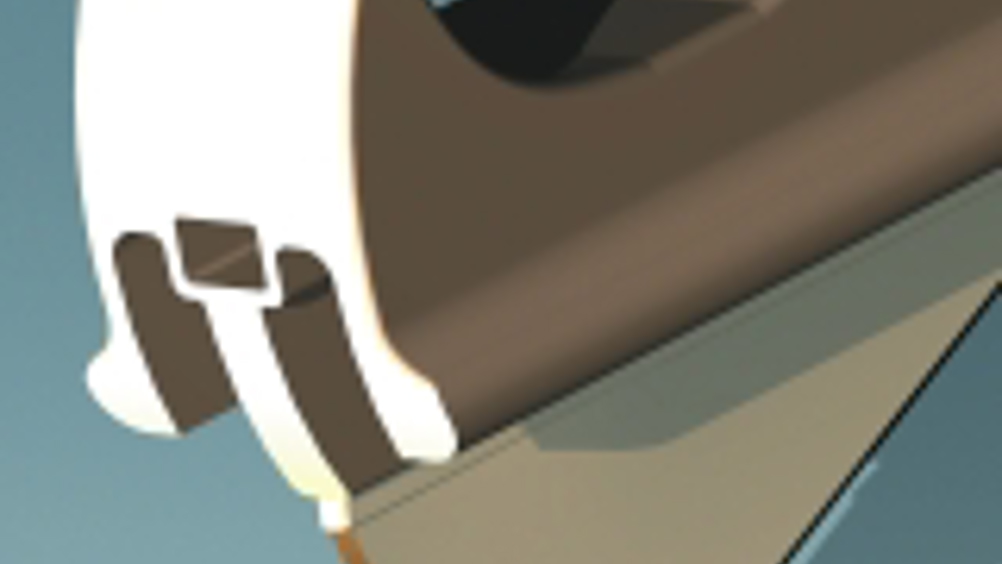
A pan-European research project has developed a way of making plastic blades for use in surgical operations.
The Disblade consortium, which includes partners from Denmark, the UK and Italy, could lead to blades that are disposed of by touching them against a hotplate – rather than being deposited in sharps bins and destroyed later.
After moulding the blade and scalpel body in a single operation, the blade is treated with a high pressure gas. This infuses ceramics into the blade to a depth of around 20 microns, giving it the necessary edge stiffness.
The partners, including Danish plastics company Rosti Technical Plastics (RTP), say that a disposable surgical blade would prevent the spread of prion proteins – which cause Creutzfeld-Jakob Disease (CJD) in humans. This is because standard sterilisation procedures do not always destroy prions.
Rosti says that the disposable devices need to be ‘low cost’ if they are to compete with traditional scalpels – but does not give exact figures.
Mike Sullivan, VP of R&D at Rosti, says: “On a one-to-one basis a steel blade could be cheaper, but on a total device basis the plastic blade is lower cost.”
The surface treatment process, called Hardplas, is complete. Rosti is still refining the way that it moulds sharp edges. Scalpels are currently made using two-shot injection moulding – with the moulding of the sharp edge quite different to that of the scalpel body.
“The blade has very fine detail to be formed within the tool, and extremely accurate flow timing and venting have to be allowed for,” says Sullivan.
The technique could be used to produce other medical products, such as ‘fingerprick’ lancets for blood tests. Rosti is also looking at applications outside the medical field.
“We are working on industrial applications, particularly to reduce the cost of components subject to long-term wear,” says Mike Sullivan, VP of R&D at Rosti Technical Plastics. “We intend to develop plastic disposable sharps for food preparation and consumer products.”
Examples include blades for food processors and lawn mowers.
The Disblade project was initially part-funded by the EU’s Sixth Framework Programme for two years. Since this ended in mid-2006, many of the partners – including Rosti, The National Institute of Technology in Norway, UK clinical product development company Clinipart and UK research organisation Pera – have continued the research.
Rosti has created a pilot plant to develop specific applications of the technology, designing equipment to increase throughput and reduce production costs. It is also testing the process on a wider range of materials.
“We are undertaking feasibility studies for major brands to mould sharps other than scalpels,” says Sullivan. “There are many industrial components which have ‘sharp’ geometry.”
POINTERS
Surface hardening technique can make plastic hard enough to be used as a scalpel
Moulding of the polymer blade continues to be improved. It is currently incorporated into the scalpel body using a two-shot process
Other potential applications include blades for food processors and lawn mowers