Light touch
Advancing production technology, and an ability to make products with less environmental impact are helping to boost the use of aluminium. Jonathan Ward reports
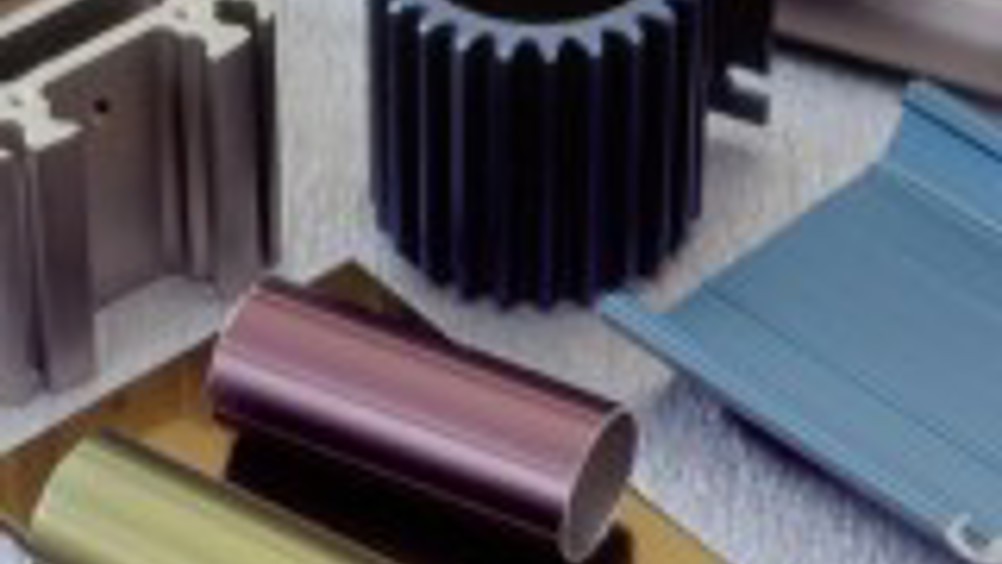
Light in weight, strong, corrosion-resistant and easily recyclable: aluminium alloys have a range of characteristics that make them highly appealing in many engineering applications. While perceived environmental benefits may be driving the uptake of the material right now, it is advanced design, production and assembly technologies that are making the material quicker, cheaper and easier to use than ever before.
One production technology delivers the benefits of aluminium in a particularly neat way. Extrusion – the forcing of heated material through a steel die – allows prismatic shapes of very high complexity to be produced at low cost.
“The tooling cost for aluminium extrusion is lower than for almost any other production process,” explains Geoffrey Doyle, technical consultant for The Power of Aluminium, an industry-funded scheme that aims to promote the use of aluminium and extruded aluminium products. “Extrusion die costs start at around £1,000. Other processes typically cost ten or even a hundred times as much.”
Advances in die design have made the extrusion process even more versatile in recent years. “Extrusion die design used to be something of an art or craft,” says Doyle. “But thanks to advances in materials, production equipment and simulation technology, it is now possible to make much more complex shapes successfully.”
As an example, Doyle shows a very fine heat exchanger part around 1.5mm thick and 40 mm wide. “Earlier versions of this would have been probably 5mm thick, with four or five mandrels [needed to make enclosed holes] in a single part. This one has more than 30 circular holes, each one less than a millimetre in diameter.”
Peter Raine, a design draughtsman for Hydro Aluminium, one of the major extruders operating in the UK, is equally enthusiastic about the properties of the process, but urges caution from designers.
“The customer typically wants the thinnest, lightest, strongest part, with the best surface finish,” he says. “You can achieve all those characteristics with an extrusion, but some of them may conflict. It can be difficult to get a good surface finish on really thin walled parts, for example.”
The best way to understand the advantages of aluminium extrusion, adds Raine, is to take a walk round an extrusion plant. “You learn more in an hour’s visit to an extrusion plant – by seeing the wide range of different shapes being manufactured – than in any amount of reading or discussion. Customers often get inspiration for entirely different applications after a plant tour.”
Part of Raine’s role is to help customers to optimise their designs to suit the properties of the extrusion process.
“If a customer is replacing a machined part with an extruded one, they have to realise that extruding won’t deliver machining tolerances,” he says. “The standard tolerances are good and, with the right design, you can control some tolerances even more tightly. But you still have to design for the capabilities of the process.”
Fortunately for designers, new manufacturing processes are extending the capabilities of that process all the time. While most parts extruded in the UK must fit through a 6inch or 8inch die, it is becoming increasingly common to assemble multiple extrusions into larger components.
“The car industry’s uptake of aluminium for structural applications has really helped to increase confidence in aluminium-joining processes,” says Doyle. “The design of adhesive bonded joints is now very well understood and widely used.”
Another new joining technology making significant inroads commercially is friction stir welding. An innovative technique developed in the UK by TWI, it uses a rapidly rotating tool to weld together two butted plates. The process is quick and results in little distortion of the joined parts. It is not straightforward to adopt, however.
“You do need to hold the parts together with large clamping forces during joining,” explains Doyle. “So the investment in tooling is quite significant.”
Cast solutions
Extrusion may be quick and flexible, but it is far from the only way to build an aluminium part. Casting still has an essential role to play, particularly for components that do not lend themselves to prismatic shapes. It may be one of the oldest metalworking processes of all, but new technology is having a big effect on the way cast parts are developed today.
Hamlin RPD, based in Offchurch, Warwickshire, has specialised in the production of prototype parts for a broad range of industries for the past 20 years. Among other technologies, the company operates a highly sophisticated flask-casting process, used for the rapid production of small batch and prototype aluminium castings.
Like traditional investment casting, the system starts with a wax model of the part to be cast. “Most commonly, we make these directly from CAD data, using one of our rapid prototyping machines,” explains managing director Karl Hamlin. “But for some larger volume parts, we also machine our own aluminium moulds for the wax.”
Hamlin technicians take the wax parts and build them into a tree with wax runners and risers to allow smooth metal flow. The whole assembly is then placed in a flask under vacuum and filled with a ceramic slurry.
“By doing the whole process in a vacuum, you make sure there are no unwanted voids,” says Hamlin. “It is also faster than the repeated dipping that traditional investment foundries use.”
The ceramic mould is fired at high temperature to solidify it and to burn out the original wax. It is then placed in another evacuated chamber and filled with liquid aluminium. Gravity and an extra boost from an injection of nitrogen behind the aluminium ensure that the mould cavity fills perfectly, with minimum porosity.
Typically, the company will take three to five days from receipt of data to production of a finished cast part. “The big advantage of the process is that the properties of the part you get out are extremely close to those of die cast components,” explains Hamlin. “Customers can take our parts and use them for full-scale testing before they make the very high investment needed for steel dies.”
Whatever the production process, aluminium’s benefits seem set to ensure that the material will continue to find applications. Designers can benefit from attractive surface finishes and new freedoms to produce complex parts. Production engineers can relish low costs and simple, rapid supply chains. As the use of recycled material becomes more widespread, the environment may enjoy some benefits, too.
It’s a Sert
Aluminium giant Alcoa has been busy devising new solutions for one of the most traditional ways of joining aluminium. The company has developed a new thread-forming insert for the material, designed to cut installation time and improve reliability.
The SmartSert, developed in Australia by Alcoa’s fastening systems business, is a high-strength threaded insert that can be installed in a hole in aluminium or plastic materials, without the need to cut an appropriate thread first. To develop the new insert, Alcoa Fastening Systems (AFS) used its experience in wire forming to produce an insert with a special concave cross section.
“The insert doesn’t actually cut the base material when it’s installed,” says Simon Bowen, director of operations for AFS Australia. “Instead, the material flows around the insert, just like modelling clay does when you press a finger into it. This eliminates cracking and other damage.”