Polyamide used for e-motor end laminate in new ABS pump
A polyamide is being used for the first time inside cars in an automatic braking system pump motor, maintaining dimensional stability up to 290°C. Dean Palmer reports
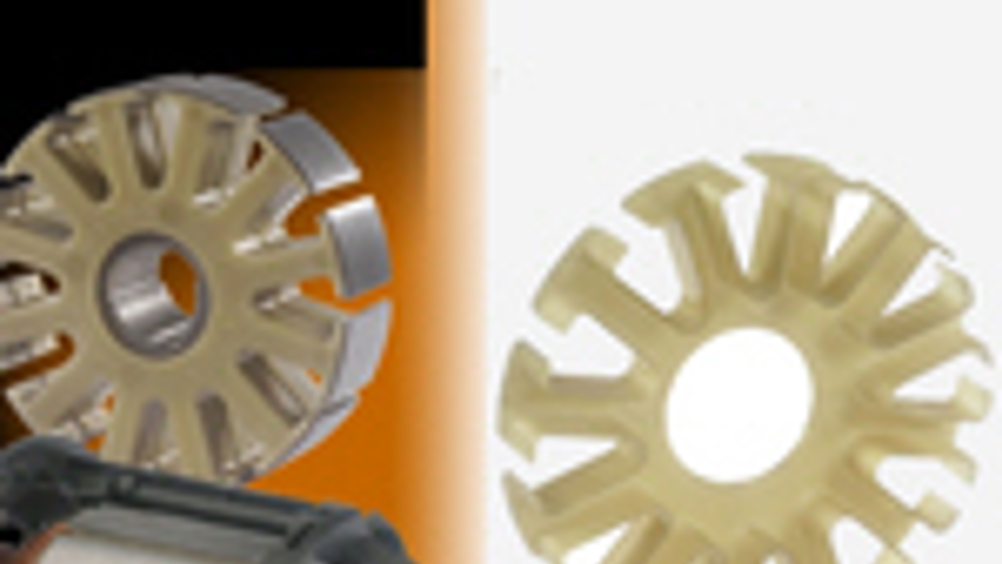
A polyamide is being used for the first time inside cars in an automatic braking system pump motor, maintaining dimensional stability up to 290°C. Dean Palmer reports
Although polyamide is often used in non-automotive e-motor end laminates because of its thin-wall strength and resistance to heat, the polymer is now finding its way into in-car applications too.
Siemens VDO, for example, is using Stanyl polyamide 46 (PA46), from DSM Engineering Plastics, for its new pump motor for an automatic braking system (ABS) on passenger vehicles.
In the new, compact DC e-motor, Stanyl resin enabled an ultra-thin wall (0.4 to 0.6mm) design that maximised both the laminate size and the number of wire windings. It provides a cost effective way to optimise the motor assembly process, while insulating the wire windings electrically from the metal rotor armature. The Stanyl end laminate retains working rigidity and dimensional stability up to 290°C, higher than most thermoplastics subjected to wire winding tension load.
In DC e-motors, wire windings around a metal rotor induce a magnetic flux. This energy causes the motor armature to rotate within an encompassing magnetic field, normally provided by permanent magnets located around the armature. According to DSM Engineering Plastics, using Stanyl enabled thinner end laminates , resulting in a more stable winding process, or larger e-motor sizes suited for cost effective usage of end laminates. Ultra-thin end laminates, which position and insulate the wires using the smallest possible volume, help reduce assembly and system costs due to excellent toughness and flow of the material.
"When Siemens VDO engineers began the search for the right material, they were aware of Stanyl's suitability for high heat applications as a result of the company's long-standing collaborative relationship with DSM," said Richard Frissen, ADTS manager automotive at DSM Engineering Plastics. "Together, we were able to design the right end laminate for this need, one that provides a good balance of economics and rigorous functionality."