Advances in PLM help get more products to market more quickly
For some engineers, the value of PLM can be difficult to grasp. It can be viewed as somewhat bureaucratic, creating procedures that are more about measuring performance, managing change, and handling production than innovation, design and actually adding value. It is criticised for stifling creativity and taking up time that would be better spent elsewhere. But here is the rub: PLM is not all about engineers.
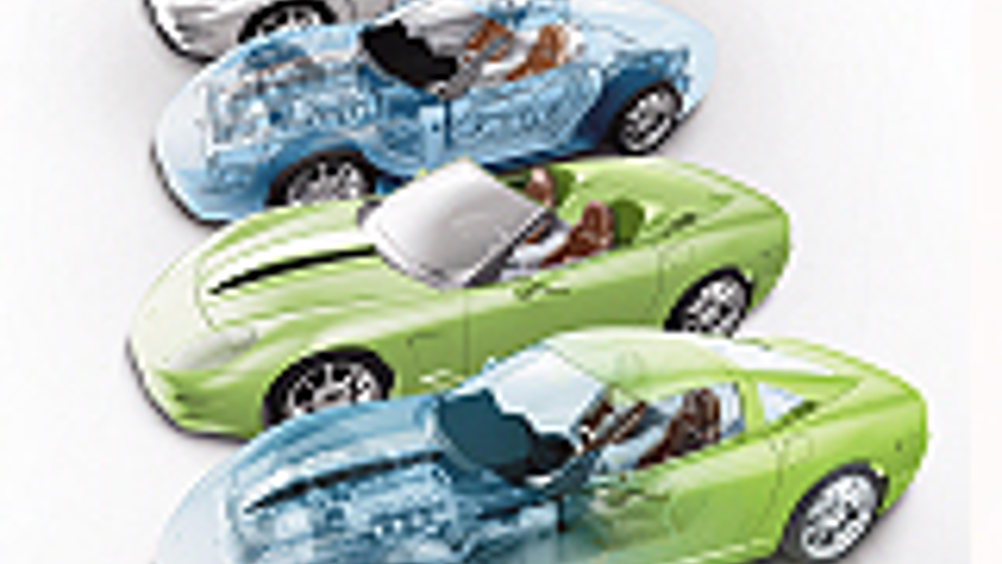
Ultimately, it is about getting better products to market more quickly and efficiently. Like much of the western world, the UK has come under intense commercial pressure in recent years as emerging economies continue to compete with a vengeance. Western companies need to be more efficient and they need to be smarter. And that means leveraging and exploiting technology and systems like PLM.
The CAD and PLM giants are now producing extremely powerful software that can be integrated throughout enterprises to capture data and use it to improve design. So what does this actually mean in practical terms?
Potentially, it means that the knowledge of a manager at a department or sites can be shared much more easily; that expertise and ideas from engineers can be captured; and that information traditionally exchanged around the coffee machine or across desks can be digitised and made globally available.
As romantic as all this might sound, PLM is actually at the stage where this seemingly peripheral data can increasingly be leveraged as an asset. If a service engineer in a remote region has an idea to improve the design to make maintenance easier, it is not lost. Strategic business and engineering recommendations are not lost in the pages of an annual report. Everyone, for example, who needs to access what a design department across the other side of the world is up to can do so quickly and easily. It also means local preferences and influences are replaced with more standardised parts and platforms.
The best strategic decisions come from those that know what is happening on the ground. And PLM is about unlocking what line managers and engineers know, so decision makers can understand the issues, hear the recommendations and make good strategic decisions for the business, and react more quickly.
At the recent Planet PTC Live world user conference, the company went to great lengths to get its customers to exploit the capability of its software more fully.
What is all about engineers is design software and it is clear that PTC is placing high hopes on the recent release of its CAD package, Creo 2.0, to overcome many of the previous issues with Pro/Engineer. It is more intuitive and easier to use and incorporates different approaches from 2D sketching to direct modelling to parametric modelling, to accommodate the different types and stages of the design process. PTC says Creo 2.0 is in a much better position to support the trending design and business philosophy of engineering more variants from fewer platforms.
"Almost half of our customers say this is a key strategy going forward. It is a business priority to reuse common platforms and modules," says Mike Campbell, division general manager of CAD, at PTC. "If you are going to meet today's demanding challenges around time to market, you have got to be able to quickly reuse and repurpose existing 3D geometry."
In response to this, PTC has introduced the Creo Options Modeller. This application is specifically built for designers and engineers who need to validate and reuse 3D digital definitions of configurable products early in the design process.
At present, many designers use a workaround in Pro/Engineer or another CAD system by building up a single 'super assembly' – often called an 'overloaded assembly'. This uses every possible component and configuration a particular product could ever have, which the designer copies and simplifies to make a variant.
Creo Options Modeller instead uses a modular assembly made up of interchangeable components that are mapped to one another. This avoids the time-consuming overloaded approach and can automatically create variants by selecting options that drive included or excluded components within a design. Designers can, however, manually override any of these options and create any combination of parts they see fit.
Speaking at the conference was appliance manufacturer Whirlpool. The company last year celebrated its 100th anniversary and is currently further implementing PLM across its organisation. It has recently released it Maytag Maxima washer and dryer which took two and half years to develop. And that, says the company, is simply not good enough.
"If we can't speed up our time to market, we don't need to be talking about our 200th anniversary, put it that way," says Jeff Burke, a director of the program management office at Whirlpool. "We want more product variants but with fewer product platforms, to be able to give our brands more differentiation to satisfy the needs of local markets, but with more standardisation so that everything else inside the product doesn't have to change."
PLM can help drive standardisation. This in turn has benefits when it comes to time to market. If parts are standardised, the supply chain is already in place, there is no need to go through a procurement process, and economies of scale help bring costs down.
"We have been able to drive some huge improvements by creating databases of parts, by organising parts and making that information available," says Burke. "It is not that engineers haven't wanted to do this before, it's just they might not have been familiar with a part or have known where to find it, so that makes it difficult.
"We have been able to reuse parts like valves, motors and engines across brands and product types. Once we have global availability of that information we can standardise it across the enterprise. Fasteners, for example, we have been working on for a long time and that is a pretty standard component. We have a good global database, so engineers in Germany or the US can't just create a fastener – they're not allowed to. They have to go to the library and if the one they need is not there, they have to request that one be created."
Requesting permission to use a fastener might seem bureaucratic to the engineer, but PLM is about standardisation and defining the boundaries for which designs can, and should, be produced. As Whirlpool continues to follow its roadmap of PLM integration, it is finding the benefits, in terms of getting more products from fewer platforms to market faster at a lower cost and at better quality. But can over-standardisation inhibit innovation as engineers feel too constrained to try anything new?
"People might have this view of PLM as a constraining force," says Fred Bellio, a chief information officer at Whirlpool. "But, there is value in a little bit of constraint, and I like to think of that as collaboration."
Bellio is an engineer and understands these qualms more than most. He says: "We do get feedback about a fear of over-bureaucracy; it is one of our biggest fears. If you look at failure modes and poor PLM implementations: if we don't do this right we are going to do exactly that, we will put too much bureaucracy on our engineers and it will fail."
While designing variants might be a fairly constrained process, Whirlpool says it wants to give more freedom to its engineers at the concept level. As long as it can get feedback in to the design loop much more quickly, it is actively encouraging its engineers to try new things.
Bellio concludes: "We can say very quickly as a company 'let's fund this idea as we think there is value in it'. We can get more ideas, focus on the right ones, put them in to the product development process, and ultimately take more variant products to market more quickly."